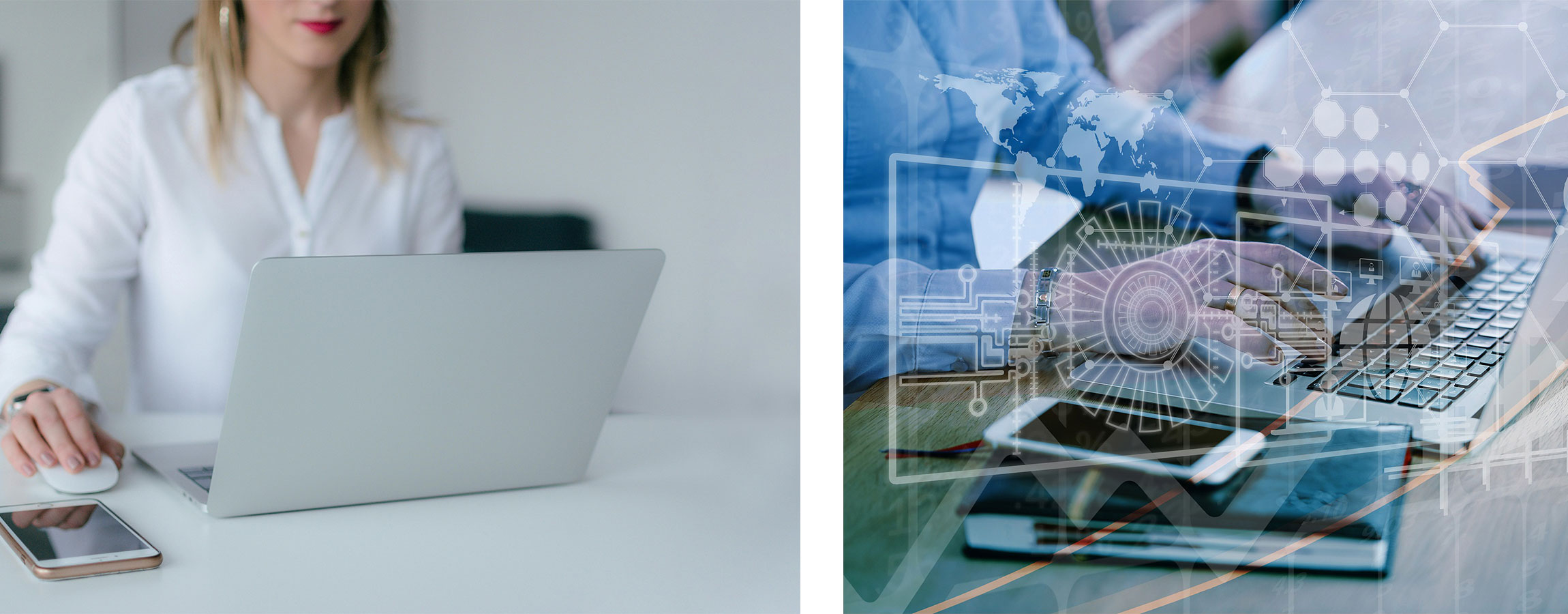
Welcome to the third installment in our “Food Safety, QMS and Environment” series. Previously, we explored our journey with ISO 9001 and ISO 14001 certifications. In this piece, we reveal how these principles are integrated into our day-to-day production operations at ASEPT International AB, featuring insights from our Operations Manager, Pia Wickenberg.
Integrating ISO 9001 Principles into Daily Operations
The guidance provided by ISO 9001 has significantly enhanced our quality initiatives. Pia Wickenberg emphasizes, “The biggest difference compared to the past is the creation of clear and documented routines and backup processes for our workflows and competencies. Our documentation of routines is no longer tied to individual ‘know-how,’ making us less vulnerable and more efficient. This improvement is a direct result of our dedicated quality work based on ISO 9001 principles.”
Documenting processes has revealed numerous opportunities for improvement, leading to a more efficient and streamlined workflow. Employee engagement has intensified, as everyone can see how their contributions make a difference in day-to-day operations.
The detailed documentation of routines also facilitates faster and more effective onboarding of new staff, allowing them to feel secure, valuable and capable of contributing in a shorter amount of time.
Customer Order Routines
One notable improvement is in our customer order routines. We’ve transitioned from email and printed paperwork to a more digital approach. Using our business system to log and track processes increases efficiency, transparency and security, enabling us to provide the best possible service to our customers. This digital shift also offers environmental benefits by reducing our reliance on printed paper.
QMS & Delivery Precision
Other enhancements achieved through ISO 9001 guidance include logging and managing all cases and issues in our Quality Management System. This structured approach minimizes the risk of overlooked issues. Additionally, we now measure Delivery Precision daily, ensuring we can meet customer expectations by planning and adjusting as needed.
Pia Wickenberg shares her enthusiasm: “What’s super fun about this work is that we genuinely want to improve our quality and processes. We have a mentality to always learn and improve. It’s not just a ‘certificate’ to us; it’s a way of working. It has given us better structure, and efficiency and has improved our operations. We have found a great balance between effort and output in our quality work!”
Stay tuned for more articles in our “Food Safety, QMS and Environment” series! Interested in our previous articles? Check them out here: ASEPT News: Your Source for Dispensing Solutions Insights